Pilot Case Acronym: FunFlex
Full name: “Surface functionalization of Circular flexible food packaging”
Company Name: LEYGATECH
Pilot Case Description:
The EU Single Use Plastic directive or the French law AGEC is increasing pressure on the plastic converters, urging them make a quick response especially on the recyclability of single use plastic products. The FUNFLEX project aims at developing and implementing novel multilayer structures based on the use of advanced coating or nanolayer that ultimately will insure recyclability to single-use food packaging solutions. Using available surface treatment technologies, barrier capabilities will be brought to an eco-designed structure that is able to replace actual state of the art, unrecyclable, packaging. Should it be realized by means of coating or plasma deposition technology, these techniques still misses the final industrialization step. Finally, the developed solutions will undergo LCA studies as well as recycling and food contact certification to prove that they have a positive environmental impact and that they do not diminish the waste recovery efficiency. The achievement of the objectives will allow to demonstrate the feasibility of ready to recycle packaging for applications such as tray lids, snacks packaging, high output pouch making and many others. Those achievements will first insure a stronger competitiveness of the company but also insure the commercialization of products that would have been banned in 2025 if not recyclable.
In order to execute this Pilot Case, LEYGATECH used the combined services of FlexFunction2Sustain consortium partners Fraunhofer Institute for Organic Electronics, Electron Beam and Plasma Technology FEP and Fraunhofer Institute for Process Engineering and Packaging IVV, IPC – Centre Technique Industriel de la Plasturgie et des Composites, INL International Iberian Nanotechnology Laboratory & Sonnenberg Harrison Partnerschaft:
- Development of PE functionalization;
- Evaluation of the solutions and validation of the best structure;
- Compliance with standards, Food contact assessment and Intellectual Property analysis.
- Introduction: https://flexfunction2sustain.eu/funflex-pilot-case-introduction/
- Completion: https://www.youtube.com/watch?v=3zCAN7di8Sk
Pilot Case Acronym: SUSTAINPACK
Full name: “Sustainable packaging”
Company Name: HPX Polymers
Pilot Case Description:
We are developing bio-degradable and/or bio-based packaging concepts, which are fully recyclable, with different industrial customers and production partners. One of the possible concepts (#1) is based on a combination of a barrier coated bio-polymer laminated to a stiff paper using a polyvinyl alcohol (PVOH) that improves the oxygen barrier and at the same time offers a degradable and soluble layer. Another concept (#2) is the co-extrusion of a bio-polymer film with PVOH core, to increase the oxygen barrier and allows a biodegradable and recyclable polymer film. One other possibility (#3) would be the combination of co-extruded polymer layers with a PVOH barrier layer in between. This will allow easy recycling of the different polymers used on the different outer sides for the optimization of the mechanical and barrier behaviour of the whole film combination e.g. one side PE for maximum water vapour barrier the other side PBS or PET with improved oxygen barrier and for mechanical stability and or reverse printing. The PVOH layer would dissolves in water during the pre-treatment step of recycling, and the laminate debonds. By this way, PBS or PET and PE layers are easily separated via density, leading to clean fractions of PVOH solution, PET or PBS, and PE for direct mechanical recycling process. One last approach (#4) is mono-layer film suitable for thermoforming providing biodegradability, recyclability and improved barrier.
The aim of this project is to find out the suitable PVOH formulation. This requires deep understanding and therefore investigations of viscosity, layer thickness, additives for adhesion and extrusion versus solubility of the PVOH. Different series of product demonstrators are to be produced based on these basic combinations.
In order to execute this Pilot Case, HPX Polymers used the combined services of FlexFunction2Sustain consortium partners Fraunhofer Institute for Process Engineering and Packaging IVV, Fraunhofer Institute for Organic Electronics, Electron Beam and Plasma Technology FEP, IPC – Centre Technique Industriel de la Plasturgie et des Composites, COATEMA, INL – International Iberian Nanotechnology Laboratory:
- PVOH-based adhesives cannot be used on a classical lamination line. Without the solvent, i.e. water, PVOH loses its tackiness and adhesion, so a “wet” lamination with following drying step is essential. This cannot be offered on a classical solvent based lamination line, which typically first dries the adhesive, and then is laminating this very sticky adhesive layer against the second solid layer e. g. paper.
- For Co-extruded blown or cast films, extrudable PVOH-compounds need to be developed. Due to the solubility, PVOH cannot be compounded on classical compounding lines using under waterbath granulation.
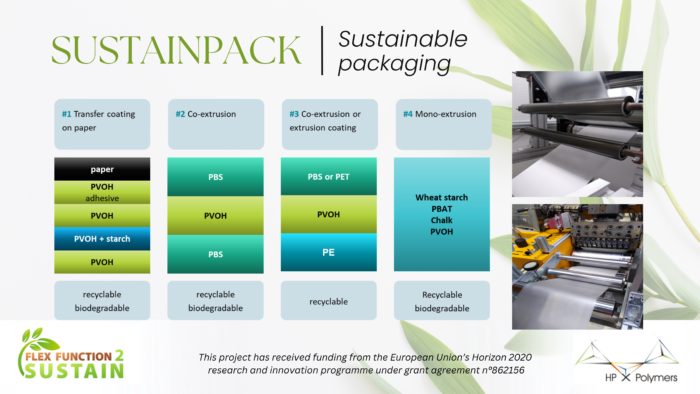
- Introduction: https://flexfunction2sustain.eu/sustainpack-pilot-case-introduction/
- Completion: https://youtu.be/XgaEVlJ-jRo
Pilot Case Acronym: IDOLES
Full name: “Improvement of durability by optimizing Low Energy Surface”
Company Name: Infrascreen
Pilot Case Description:
Today, transparent curtains are used in greenhouses to save heat during winter. These curtains act as a transparent insulation layer reducing heat loss by convection. Infrascreen is developing an innovative curtain that saves an extra 15-20% of heat. For growers that means direct costs savings and CO2 emissions reduction, because most use natural gas to heat their greenhouses. Our solution has an environmental impact of ~120 tons of CO2 emissions saved per 10’000 m2 of greenhouse each year. For our project with FlexFunction2Sustain, we want to evaluate different protections. We will need to (1) understand the interface between the protection and the film (2) assess the stability in time of the protection (with regards to humidity, UV and chemicals used for plant protection) and (3) explore relevant blocking and other third-party IP and freedom to operate for the protection.
In order to execute this Pilot Case, Infrascreen used the combined services of FlexFunction2Sustain consortium partners Fraunhofer Institute for Organic Electronics, Electron Beam and Plasma Technology FEP, Joanneum Research, Aristotle University of Thessaloniki, INL – International Iberian Nanotechnology Laboratory, Sonnenberg Harrison Partnerschaft:
- Corrosion protection coatings on sheets;
- Surface and layer characterization;
- Review of the final product specifications of corrosion protection coatings and methods of manufacture of these coatings, including structuring. Identification of relevant granted patents and pending patent applications with focus on Europe.
Pilot Case Acronym: POSIDONIA
Company Name: PHEE private company
Pilot Case Description:
Exterior decorative panels are used for aesthetic reasons, temperature comfort (shading) and lighting design. The synergy of the UV radiation, elevated temperature, increased humidity and rain, create a very aggressive environment for those composite materials. Currently, phenolic based composites (HPL) are massively used in interior (wall-coverings, furniture, flooring) as well as for exterior applications on construction projects.
PHEE, a Greek materials startup, develops and produces, via an unconventional manufacturing process, bio-based composite panels by upcycling, as fillers, natural fibrous residues, such as Posidonia Oceanica dead leaves, combined with certified bio-based thermosetting resins. PHEE materials show a lower embodied carbon and toxicity in comparison with phenolic based laminates. PHEE composites fulfil industry specifications for interior applications and but there are still technical challenges to overcome for introducing materials for exterior applications where they have identified a business opportunity! Based on their market research, exterior panels are a fast-growing market currently searching for sustainable alternatives that can contribute efficiently to net-zero goals. According to Market Research Future, the HPL exterior boards market industry is projected to grow from USD 3.1 billion in 2022 to USD 4.3 billion by 2030, exhibiting a compound annual growth rate (CAGR) of 4.80% during the forecast period (2022 – 2030).
During POSIDONIA pilot case a triple-layer biocomposite material will be produced and evaluated, where the outer skins will be modified creating micro-patterns. These micropatterns provide superhydrophobic behaviour and consequently water repelling capabilities, while their material consists of bio-based polymers with advanced UV protection. The expected enhanced hydrophobic properties and UV resistance of novel biocomposites will lead to sustainable cladding and siding panels for exterior applications on construction projects introducing a economic viable with lower embodied carbon alternative to conventional phenolic based HPL’s.
In order to execute this Pilot Case, PHEE used the combined services of FlexFunction2Sustain consortium partners Aristotle University of Thessaloniki, IPC – Centre Technique Industriel de la Plasturgie et des Composites, Sonnenberg Harrison Partnerschaft:
- Development of the thermoplastic UV protective & hydrophobic film
- Production & Testing of the enhanced PHEE panels
- Feasibility Cost Analysis and IP management
Pilot Case Acronym: BIOESS
Full name: “Barrier Improved Ovtene for Environmentally Sustainable Strategies”
Company Name: ARCADIA spa
Pilot Case Description:
Nowadays multi-layer plastic packaging represents an important environmentally sustainable issue. In particular, multilayers conventional packaging are made of a high numbers of ultra-thin layers of different materials which makes the packaging very complex to recycle. Its recycling process consists in several steps requesting a great energy and work which, beside the environmental issues, make furthermore the end product more expensive. Ovtene® is a commercial plastic material, which showed interesting results in terms of food preservation, being able to better maintain the organoleptic properties. By possessing a reduced amount of plastics and being monomaterial, can be proposed as the potential best solution for environmental sustainability. The development of modified Ovtene® materials, such as a prototype with improved barrier properties through a surface treatment or a coating deposition without compromising the recyclability, could represent a potential packaging solution to be used in the market of food products preserved in MAP (Modified Atmosphere Packaging) and markets where the sensory properties play a key role and need to be preserved. Moreover, due to the unique intrinsic properties of Ovtene®, the introduction of the secondary shelf –life concept may also represent an important opportunity to be investigated. The successful prototype will be certified against reference material for environmental sustainability through LCA analysis, barrier properties, shelf-life and migration tests.
In order to execute this Pilot Case, ARCADIA used the combined services of FlexFunction2Sustain consortium partners JOANNEUM RESEARCH, INL – International Iberian Nanotechnology Laboratory, Fraunhofer Institute for Process Engineering and Packaging IVV, IPC – Centre Technique Industriel de la Plasturgie et des Composites:
- Barrier development
- Water Vapor Transmission test
- Oxygen Permeability test
- Shelf life (accellerated) test
- Migration tests (food contact certificate)
- Life Cycle Assessment
- Recyclability tests
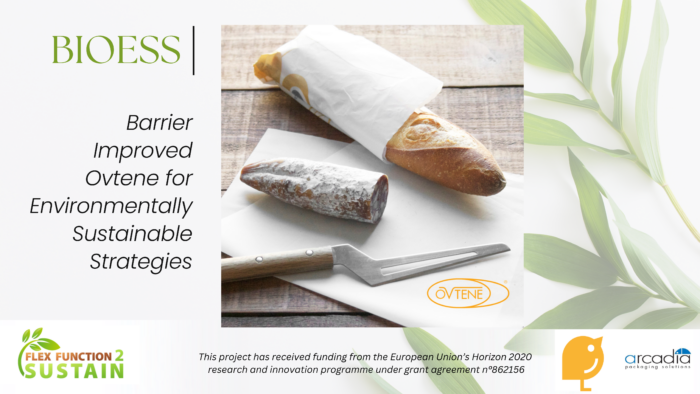
Pilot Case Acronym: ENLIGHTENMENT
Full name: “Functionalisation of agricultural films with multi-season fluorescent dye to enhanced plant development”
Company Name: CASCADE
Pilot Case Description:
CASCADE designs & develops luminescent additives integrated in greenhouse plastic films to shift a portion of the sunlight spectrum, little used by plants, into wavelengths most efficiently used for photosynthesis and plant development to improve crop yields and quality. CASCADE brings its innovation by integrating commonly used PE/EVA/PE multilayer greenhouse films with its LIGHT CASCADE® technology. Main bottlenecks of the technology are that the technology is not durable enough and shows fast decay in sunlight. CASCADE already launched on the market one-season limited photoactive additives and has developed an IP protected technology to stabilize its formulations and protect them protection against UV and oxygen by encapsulation process inserting them into a microparticle matrix.
The purpose of ENLIGHTENMENT project is to extend sunlight wavelength conversion capability of CASCADE doped greenhouse films to produce multi-season films that can enhance plant development. This can be done by integrating newly developed CASCADE protected technology into greenhouse films. More than 100 agronomic trials, carried out by CASCADE over past 9 years with its one-season technology have shown significant agronomic benefits that improve the sustainability of crop production systems such as yield gains of 10%, saving of fertilizers and water, precocity, better plant resistance to pest & disease. Moreover, an eco-design approach will be followed to ensure fully recyclable structure based on a mono-material film.
Though CASCADE long-life technology is ready to market, upscaling issues still exist. The dispersion of the microparticles in the film polymer matrix is not straightforward and agglomeration issues are observed, and issues exist regarding the film manufacturing process as some negative effects occurred when extruded at very high temperature. The ENLIGHTENMENT project will be organized around two parts, the compounding process optimization to increase the density particles in different matrices and the upscale of the multilayer films integrating the innovation at TRL7.
In order to execute this Pilot Case, CASCADE used the combined services of FlexFunction2Sustain consortium partners INL – International Iberian Nanotechnology Laboratory, Fraunhofer Institute for Process Engineering and Packaging IVV, Fraunhofer Institute for Applied Polymer Research IAP, IPC – Centre Technique Industriel de la Plasturgie et des Composites:
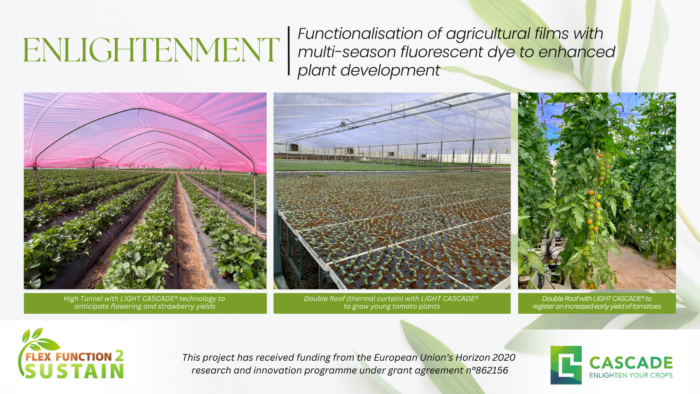
Pilot Case Acronym: RECYBIB
Full name: “Fully Recyclable Monomaterial Bag-in-Box”
Company Name: Smurfit Kappa
Pilot Case Description:
The objective is to develop a monomaterial polyethylene (PE) bag in box with oxygen barrier properties, but without EVOH. EVOH is very sensitive to humidity, very low levels can be tolerated for recycling and the growing demand causes huge shortages.
In order to reach this objective, Smurfit Kappa needs to develop a coating or surface treatment on Polyethylene film providing an Oxygen Transmission Rate below 1 cc/24h/m2 75%HR for BIB applications. The chosen technology will need to give the wanted efficiency without impacting negatively the mechanical properties of the bag nor it’s recyclability within the flexible PE recycling stream. It will need to be produced at a reasonable cost to find its place on the market.
The Consortium of the project will have to propose a barrier technology that can be applied on a PE film. Mechanical properties, barrier properties and food safety compliance will have to be evaluated by the Consortium and Smurfit Kappa. Samples of the barrier film will have to be produced, then transformed into a BIB by welding the film in the shape of a bag including the gland/tap association. The monomaterial gland and tap has already been developed by Smurfit Kappa and is at the step of consumer test. Nevertheless, one part of the tap, the membrane remains in elastomer and therefore needs to be changed in order to have a real fully monomaterial tap. But this is very challenging as it’s one of the most important parts of the BIB, responsible to prevent the leakage of the tap.
The recyclability of this innovative BIB will have to be evaluated using a recyclability pilot plant for flexible PE packaging. Evaluation methods such as Recyclass and CITEO methods will also have to be used to determine its recyclability in the various European countries. Finally, the shelf life of wine in this new packaging will have to be tested. If the work on the membrane results to be excessive for the project, it can easily be left aside to focus on the film development and tap validation.
In order to execute this Pilot Case, Smurfit Kappa used the combined services of FlexFunction2Sustain consortium partners IPC – Centre Technique Industriel de la Plasturgie et des Composites, Fraunhofer Institute for Organic Electronics, Electron Beam and Plasma Technology FEP, Fraunhofer Institute for Process Engineering and Packaging IVV, INL – International Iberian Nanotechnology Laboratory, Sonnenberg Harrison Partnerschaft:
- Production of PE rolls
- Development of an oxygen barrier coating with nano-lacquers at pilot scale
- Development of an enhanced oxygen barrier surface at pilot scale through PVD surface treatment
- Food contact assessment
- Recyclability trial
- Intellectual Property analysis
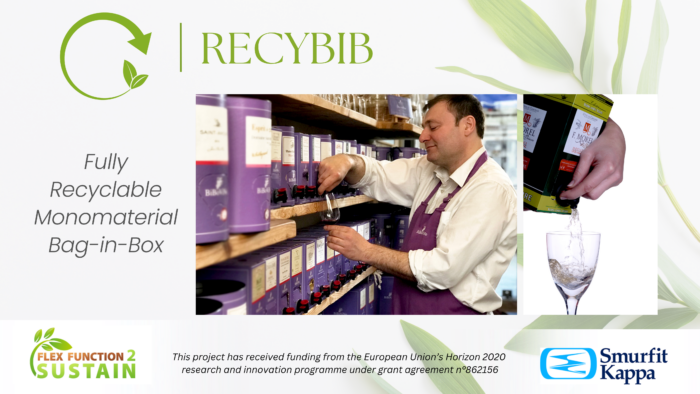
Pilot Case Acronym: AMB 2022-004
Full name: “AMB barrier film for thermoforming application”
Company Name: AMB Spa
Pilot Case Description:
AMB challenge is to identify material formulations and/or coating technologies able to provide a recyclable PET sheet, chlorine-free and halogens free, that can replace the current structures in applications where the barrier requirements are very demanding (for example in food and pharma applications), guaranteeing the same barrier levels against moisture. The PET substrate is then thermoformed to have a blister pack (bottom part of the blister), so the barrier must not be damaged with this thermo-mechanical process.
Possible solutions that could be explored in this project include the barrier development, coating technologies and formulation of PET compounds with suitable additives, provided by the Flexfunction2Sustain partners.
The project will allow AMB to have a technical solution suitable for the blister application, recyclable and aligned with EU regulation on recycling plastic, moreover, avoiding the use of components such chlorine and halogens that are dangerous for the environment.
In order to execute this Pilot Case, AMB used the combined services of FlexFunction2Sustain consortium partners Joanneum Research, IPC – Centre Technique Industriel de la Plasturgie et des Composites, Fraunhofer Institute for Organic Electronics, Electron Beam and Plasma Technology FEP, Fraunhofer Institute for Applied Polymer Research IAP, Fraunhofer Institute for Process Engineering and Packaging IVV, Sonnenberg Harrison Partnerschaft, including:
- Identification of barrier formulation and coating
- Lamination
- WVTR and OTR tests on flat films & WVTR on thermoformed samples
- Recyclability assessment
- IP and market analysis
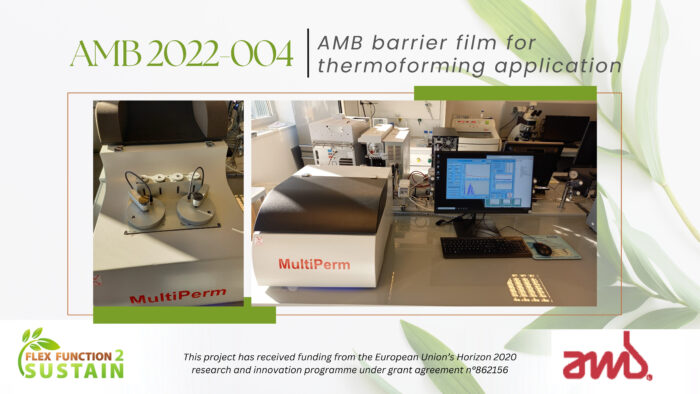
Pilot Case Acronym: RESTO
Full name: “REcycling & Sorting of plastics with Timegated Optical technology”
Company Name: SINBIOSYS SRL
Pilot Case Description:
Society is urgently asking for a more sustainable economy of plastics. In January 2021 the EU started applying an 800€/ton of plastic packaging waste that is not recycled, 4 million tons of new polypropylene (PP) are used for disposable packaging every year, 30% of that (1.2 M tons) is used for food packaging and less than 7% of this plastic is recycled for a total cost that reaches 3.2 trillion €. This situation is causing a high demand from EU converters in the packaging sector for high-quality and food-grade recycled plastics. The separation of multi-material streams into highly pure mono-material is the major issue that hinders the development of an efficient and affordable circular economy for plastics.
The novelty of our approach to tackle the problem of plastic sorting and to reach the target of mono-fractional composition of plastic waste is the use of silicon quantum dots (SiQDs). They are invisible inks: colourless under sunlight, and brightly emitting upon UV excitation. The colour of the emission can be tuned by changing the nanoparticle size. Each plastic material (or grade within the same material) can then be coded with a different combination of markers, producing a so-called luminescent fingerprint.
Within the FlexFunction2Sustain project, we aim to:
- Asses LCA of luminescent marked polymers packaging, in collaboration with SimaPro;
- Test high throughput compounding of nano-marked polypropylene at Meteor facilities;
- Asses comprehensive qualification of plastic waste down to the complete technical data sheet of the recycled materials;
- Leverage the food packaging plant and food contact laboratory to achieve FCM characterization with toxicological analysis of our nanomaterials and imaging of nanomaterial-cell interactions.
The final prototype will be a polypropylene packaging batch (flexible pouches and thermoformed cups) with SiQDs embedded that will enable efficient sorting. The prototype shall meet full recyclability in the flexible PP stream food contact expectation, and improve sorting efficiency.
In order to execute this Pilot Case, SINBIOSYS used the combined services of FlexFunction2Sustain consortium partners IPC – Centre Technique Industriel de la Plasturgie et des Composites, Fraunhofer Institute for Applied Polymer Research IAP, Fraunhofer Institute for Process Engineering and Packaging IVV, INL – International Iberian Nanotechnology Laboratory, Aristotle University of Thessaloniki, Sonnenberg Harrison Partnerschaft.
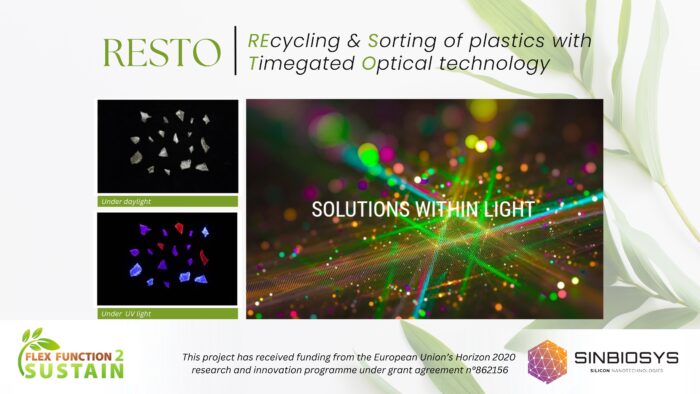
Pilot Case Acronym: AGRILOOP
Company Name: Groupe Barbier
Pilot Case Description:
The BARBIER Group is the leading producer of polyethylene films for agriculture, industry and trade applications. While the majority of films produced for the agriculture market are monomaterials, based on Polyethylene (PE), some applications require complex structures to provide gas barrier properties to the films: for markets such as silage and soil disinfection films, the demand is increasingly moving towards technical films made up of multilayer films therefore combining several polymers: PE/EVOH/PE, PE/PA. These multilayer films, being hardly recyclable, are currently mostly landfilled or burned into energy.
AGRILOOP intends to validate the recyclability and the circularity of PE/EVOH and PE/PA agricultural films while keeping barrier and mechanical properties, using METEOR’s pilot line technology from IPC. The objective is also to validate the replication of the production concept to a two steps process approach where the compounds produced by the METEOR technologies is shipped to an external blown extrusion line, as well as in a tri-layers blown extrusion line with recycled layer in between two layers of virgin PE.
The project will increase circularity of PE/EVOH and PE/PA agricultural films, in line with EU objectives to incorporate 30% of recycled materials in products by 2030 and improve the valorisation of PE/EVOH and PE/PA agricultural films to avoid down cycling, and improve the environmental footprint.
In order to execute this Pilot Case, Barbier Group used the combined services of FlexFunction2Sustain consortium partners IPC – Centre Technique Industriel de la Plasturgie et des Composites, Fraunhofer Institute for Applied Polymer Research IAP, INL – International Iberian Nanotechnology Laboratory, Sonnenberg Harrison Partnerschaft.
- Material preparation and compounding studies
- Film production (Direct compounding-extrusion & Single layer blown film extrusion)
- Recyclability evaluation
- Film characterization
- Food contact assessment
- LCA analysis
- IP analysis
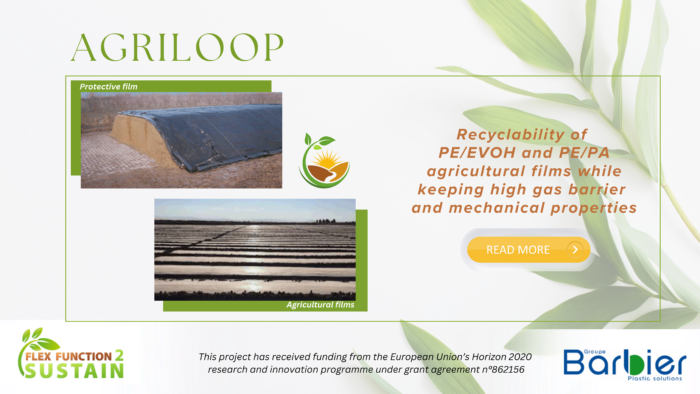
Pilot CaseAcronym: POSEIDON
Full name: “Pouch made of cellulose for liquid container applications”
Company Name: ARJOWIGGINS
Pilot Case Description:
The extensive pressure on Single Use Plastic coming either from the EU directive or the French law AGEC
is pushing packaging providers to consider paper solution where plastics were originally the only economical
solution.
Produced by ARJOWIGGINS, Sylvicta paper is a clean paper with natural bonding and exceptional barrier
properties, created by taking virgin wood pulp fibres to a microscale. Sylvicta paper has already a Moisture
Vapour Transmission Rate (WVTR) lower than 100 g / (m².day) and a good oxygen barrier that make it an
exceptional candidate for food packaging. By adding a low WVTR coating (with a WVTR value of 10-100
g/m²/day), it is used to make pouches for food that is dry or humid.
The goal of POSEIDON project is to develop a novel structure based on Sylvicta paper with the integration
of an additional barrier layer that can increase the moisture vapour barrier to be able to access liquid food
packaging and compete with the actual structure made of a complex of plastics and aluminium. The ultimate
goal is then to have a fully recyclable and compostable paper-based beverage packaging. Indeed, the demonstrator developed will tackle the problematic of beverage packaging (pouch) as faced by the industry today. Using available surface treatment technologies, functions will be added to keep the paperbased solutions recyclable.
Finally, the developed solutions will undergo LCA as well as LCC studies to prove that they have a positive
environmental impact and that they match the market prices expectations. The new structure will meet the recyclability standard ISO 13430 for paper and board recycling and will be upscaled to pilot scale.
In order to execute this Pilot Case, ARJOWIGGINS used the combined services of FlexFunction2Sustain consortium partner: IPC – Centre Technique Industriel de la Plasturgie et des Composites, Fraunhofer Institute for Process Engineering and Packaging IVV, Fraunhofer Institute for Organic Electronics, Electron Beam and Plasma Technology FEP, INL – International Iberian Nanotechnology Laboratory, Sonnenberg Harrison Partnerschaft.
Pilot Case Acronym: BB-BROF
Full name: “Biobased high refractive optical film”
Company Name: Bruno Bock GmbH
Pilot Case Description:
The Bruno Bock Group is the world leader in providing high-quality organosulfur solutions for a broad variety of applications. The polythiols made by Bruno Bock and used in high index optical films are currently made unsustainably from petrochemicals. Our objective is to create transparent high refractive index films made from bio-based raw materials (minimum 60% biobased content). We propose to use the same Thiol-Ene chemistry as current, combining biobased Ene components with polythiols that will be synthesized from raw materials issued from renewable biomass. The resulting biobased UV-curable films will be used in various optical applications. Through the services offered by the FlexFunction2sustain project, we will be able to develop and test the films and generate LCA data for these new biobased materials.
In order to execute the Pilot Case, Bruno Bock GmbH used the combined services of FlexFunction2Sustain consortium partner: Joanneum Research, Fraunhofer Institute for Process Engineering and Packaging IVV, IPC – Centre Technique Industriel de la Plasturgie et des Composites, Sonnenberg Harrison Partners, which include:
- Polymerization of polythiols with itaconates using biobased initiators
- Development of the high R.I. optical film
- Alternative thermoplastic materials for injection molding
- Mechanical tests on film
- Optical tests on polymers and films
- Life Cycle Assessment
- Freedom to Operate (FTO) search and IP protection strategy
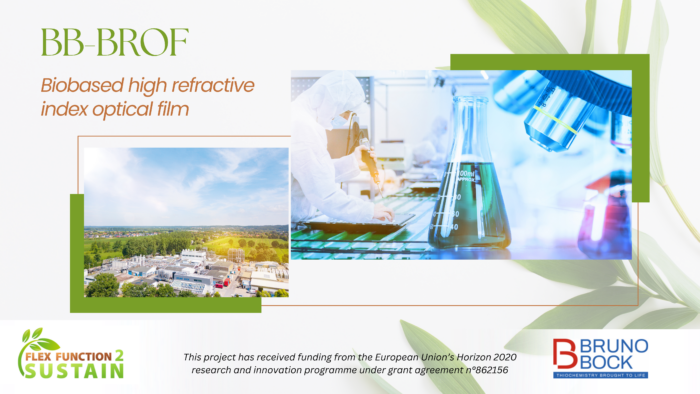
Pilot Case Acronym: P.L.
Full name: “PETLoop”
Company Name: TRANSPARENT PAPER LTD
Pilot Case Description:
The increased need for recyclability of flexible packaging requires a structure simplification while preserving the essential functionalities to keep the packaged product safe for the consumer. In this context, high gas barrier layers in packaging must be fully compatible with large-scale recycling. To date, there are few alternatives to non-recyclable barrier layers with PET such as PVDC, Nylon or EVOH or recyclable but sensitive to elongation and scratches such as AlOx and SiOx coating.
A high gas barrier thin coating with lower sensitivity to mechanical constraints and that would preserve the recyclability of the polyester packaging by mechanical means that it would be a breakthrough on the flexible packaging market. The Polyplex prototype will consist of a primed bioriented polyester film on which the Fraunhofer coating, BarriLac, will be applied. This film will then be laminated with an adhesive to one or more other polyester films that will provide other functionality such as sealability. From this laminate flexible pouches and PET tray lids will be produced. In addition, FF2S will provide expertise, lab facilities for barrier testing and recycling tests for mono PET laminated structure will help to speed up the qualification process of PET films with nano coating and to enter faster in further development phases as well as migration test for food contact validation.
In order to execute this Pilot Case, Transparent Paper used the combined services of FlexFunction2Sustain consortium partner: IPC – Centre Technique Industriel de la Plasturgie et des Composites, Fraunhofer Institute for Applied Polymer Research IAP, Fraunhofer Institute for Process Engineering and Packaging IVV, INL – International Iberian Nanotechnology Laboratory, Aristotle University of Thessaloniki, Sonnenberg Harrison Partnerschaft.
- Development of a water vapor barrier coating with nano-lacquer at pilot scale
- Coating characterization
- Upscale trials
- Recyclability evaluation
- PET crystallization
- Food contact assessment
- LCA analysis
- IP analysis
Pilot Case Acronym: TORAYFAN+
Full name: “OPP mono-material structure for food packaging”
Company Name: Toray Films Europe
Pilot Case Description:
To address a specific need for food packaging which requires a transparent high barrier that is recyclable, TORAY needs the following solutions for bioriented polypropylene (BOPP) films.
The TORAYFAN+ Pilot Case aims to develop a monomaterial BoPP film with metallization or surface treatment that is fully recyclable. This innovative solution is intended to address the challenge of achieving barrier properties equivalent to Al foil through a surface treatment of PP, to enable its recyclability.
To meet this objective, Toray proposes to integrate their latest development with the FlexFunction2Sustain project. This collaboration aims to create a high barrier film for their bioriented polypropylene films, leveraging Toray’s expertise and incorporating their latest innovation.
Toray has a strong track record of innovation in bioriented polypropylene films, striving to introduce new films suitable for use as mono-materials in packaging. They propose three distinct tracks to attain all the necessary properties for the packaging application for high barrier, but also to keep properties after retort, for sealing, for ink adhesion and for the machinability.”.
In order to execute this Pilot Case, TORAYFAN+ used the combined services of FlexFunction2Sustain consortium partner: IPC – Centre Technique Industriel de la Plasturgie et des Composites, Fraunhofer Institute for Process Engineering and Packaging IVV, Fraunhofer Institute for Organic Electronics, Electron Beam and Plasma Technology FEP, INL – International Iberian Nanotechnology Laboratory, Sonnenberg Harrison Partnerschaft.
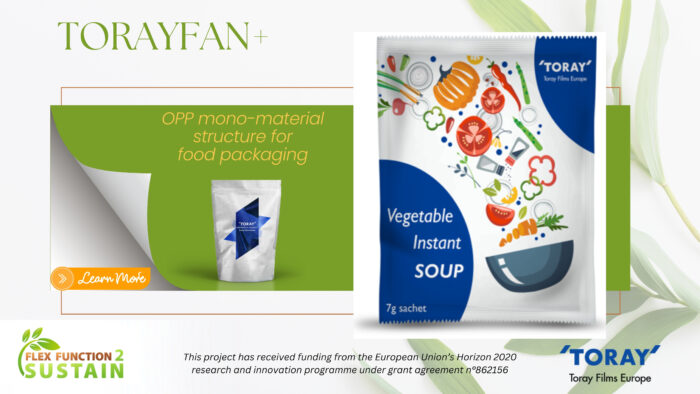
Pilot Case Acronym: LOOPTUBE
Full name: “Lamination of high barrier properties coated PE films on PE films for cosmetic tubing application”
Company Name: Albea
Pilot Case Description:
The cosmetic packaging market is under pressure from consumers awaiting new environmentally friendly products. New solutions are however only possible on the condition of overcoming key limitations: gas barrier performances today provided by aluminium or EVOH, both preventing the packaging from recycling as no separation techniques are available in a cost-efficient way.
The LOOPTUBE project will focus on the eco-design of cosmetic tubes produced from flexible PE films.
Only coating using lacquers could fit a future in-house deployment contrary to plasma based coating that will needs additional investments. To meet the cosmetic packaging market expectations, the challenge is to reach barrier properties equivalent to EVOH via a surface treatment on PE that allows its recycling. Hence, the demonstrator proposed will implement the oxygen and WV barrier coating sandwiched between extruded PE film with apply water based coating BarriLac. Later the laminate will be printed and transformed into a tube.
Ultimately, the developed solution shall meet the RECYCLASS recyclability criteria of a flexible film as well as food contact expectations.
In order to execute the Pilot Case, ALBÉA used the combined services of FlexFunction2Sustain consortium partner: IPC – Centre Technique Industriel de la Plasturgie et des Composites, Fraunhofer Institute for Process Engineering and Packaging IVV, INL – International Iberian Nanotechnology Laboratory, Sonnenberg Harrison Partnerschaft, which include coatings preparation, upscaling to final product and validation of the developed solution (Recyclability evaluation, Food contact assessment, Life Cycle Assessment, IP analysis).
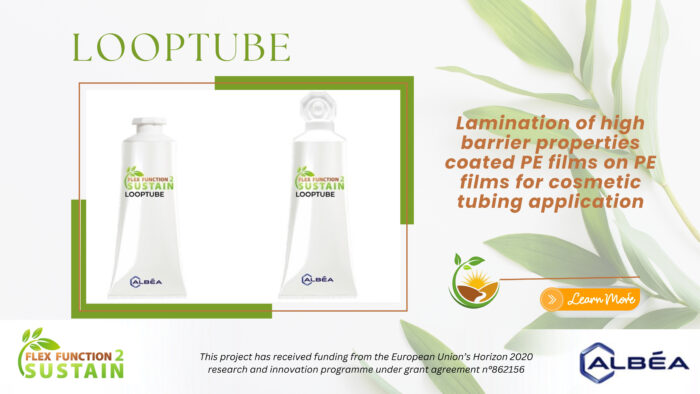
Pilot Case Acronym: BAGS4RETORT
Full name: “Mono-material plastic retort pouches”
Company Name: SDR PACK
Pilot Case Description:
The objective of this project is to develop a new monomaterial plastic retort pouch solution for food packaging. The main challenge is to identify suitable raw materials to withstand the prolonged high temperature required for the retort process. SDR PACK has been engaged to environmental and sustainability issues since years, in line with the demands of consumers and businesses. The first steps towards recyclable solutions have already been taken, by managing to ensure barrier properties, shelf-life, and machinability where possible. The FlexFunction2Sustain project will allow to identify and choose the appropriate type of plastic, adhesive, and inks.
The project will have a positive impact on the environment: the pouch will be easier to recycle because it is made from multi-layer of the same type of plastic films. The project is part of the segment of ready-to-eat and ready-to-heat-and-serve food packaging products, a sector that has seen significant development in recent years. Revenue in this industry amounts to US$77.85bn in 2022 and the market is expected to grow annually by 4%. The opportunity to develop a recyclable retort pouch meeting the requirements of the heat sterilization process would open up new advantageous opportunities. If the project will be successful, it will certainly be beneficial to increase the company know-how and to expand the sales market, also international.
In order to execute this Pilot Case, CASCADE used the combined services of FlexFunction2Sustain consortium partner Joanneum Research, IPC – Centre Technique Industriel de la Plasturgie et des Composites, Fraunhofer Institute for Process Engineering and Packaging IVV, INL – International Iberian Nanotechnology Laboratory, IPC – Centre Technique Industriel de la Plasturgie et des Composites who will perform:
- Materials identification (lacquer) & OTR and WVTR tests
- Shelf life tests
- Food contact tests
- Recyclability trials
Pilot Case Acronym: FLEX&SAFE
Full name: “Flexible Printed Electronics for wearables applications in working personnel health & safety monitor”
Company Name: Smart Engineering Management Solutions PC
Pilot Case Description:
Over the last 3 years, SEEMS has designed and developed (100% in house) its corporate Personnel Health & Safety Monitoring Device (FLEX&SAFE), as a part of its corporate aRTi-D Digital Transformation Solution, implemented with the traditional electronics approach (Rigid or Flexible PCB and SMDs). Testing through various trials (within lab and/or working environment), SEEMS found certain limitations on the Device structure itself, concerning tolerance & reliability, as well as additional requirements for more functionality to fully cover the industrial requirements. The objective of FLEX&SAFE pilot project is to upgrade the existing sensors with a new structural unit based on Flexible Organic Printed Electronics sensors (Roll-to-Roll compatible printing and materials), that will provide a robust construction, highly tolerant, to satisfy user’s comfortability & trust compliant with the required industrial standards and working requirements. This will ensure longer durability of the wearable device, better adaptability as a wearable. To achieve our objective the FLEX&SAFE sensor will be manufactured employing Printed Electronics standards & procedures, to become a highly competitive tool in Health & Safety of the working people.
In order to execute the Pilot Case, SEEMS used the combined services of FlexFunction2Sustain consortium partner: Aristotle University of Thessaloniki, Organic Electronic Technologies Private Company, Bl Nanobiomed, IPC – Centre Technique Industriel de la Plasturgie et des Composites, Sonnenberg Harrison Partnerschaft, which involve:
- Materials characterisation techniques
- Printed organic electronics sensors technology and R2R printing technologies
- Life Cycle Analysis
- Patent Search & market analysis
Stay tuned! Further details on Pilot Case development will follow.
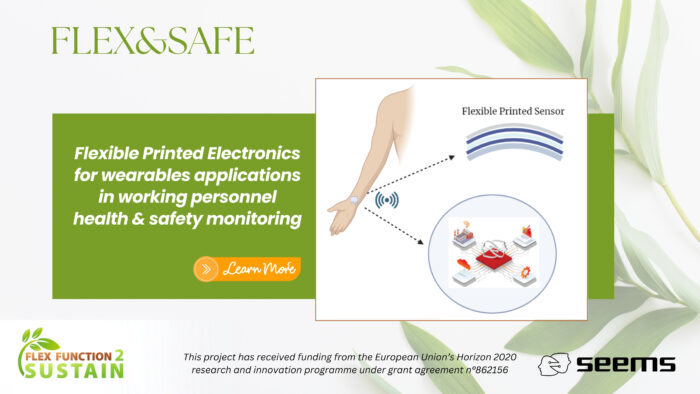